On the 10th December 2015, Evergrande GMP Dairy proudly launched its “Cowala Seamless Quality Protection Logistic System” at its state of the art new logistic centre in East Tamaki, Auckland.We were honored to have MP Mr Stuart Smith (Member of Social Service Committee, Deputy Chairperson of Primary Production Committee) & MP Mr Jamie-Lee Ross (Member of Foreign Affairs, Defense & Trade Committee and Chairperson of Parliamentary Service Commission Precincts Committee), CCIC, China Shipping NZ and various VIPs & guests join us on the day to share this special occasion. Mr Stuart Smith had especially flown from Wellington to Auckland to attend the event.
In the past year, Evergrande GMP has grown at a rapid speed. Since November 2014, Evergrande GMP has exported around 3 million cans (450 TEU) of its Cowala 900g infant & adult formula to North Asia including China and Korea. Cowala milk powders are not only consumed by around 80 thousand families in China; Cowala infant formula has also become one of the top selling New Zealand infant formula brands in Korea’s high-end supermarkets.
Evergrande GMP Dairy upholds the “Quality Above All” belief and implements the highest pharmaceutical standards for production management, which means that rapid development of production scale is matched by acceleration in product quality and product safety.
With excellent product quality and its good reputation established by consumers’ word of mouth endorsement, Cowala has been voted as “China’s most influential infant formula brand 2015” on China’s Sina network, it has also won “2015 Mummy’s most recommended imported infant formulas 2015”, a survey which was participated in and voted by thousands of mothers in China.
Evergrande GMP’s Seamless Quality Protection Logistic System
Evergrande GMP’s logistic system provides the best assurance possible that the quality of our product is maintained without compromise during its long journey from the Land of the Long White Cloud, all the way to ports in China.
It is a Seamless Quality Protection System because at every step of the way, at every product movement, every storage location, risks to product quality have been assessed and we have taken appropriate measures to eliminate or minimize those risks. There are no gaps in the process, no missing links in the chain and product quality is protected at each movement and at each storage point.
All GMP’s products are manufactured in accordance with the Risk Management Program pertaining to that site and meet all quality parameters under that RMP.
GMP’s containerization step is especially unique and innovative. GMP’s warehouse has a fully enclosed indoor area where we can position and load 8 40ft containers at once, in a fully secure environment, 100% protected from the weather.
GMP maintains an excellent relationship with shipping partners and has in place agreements whereby our containers are loaded onto container ships at or below the water line. This ensures containers are placed where they are most protected from temperature extremes which could affect the temperature-sensitive vitamins and essential fats and oils in baby formula. As an extra assurance, every container carries a temperature data logger, which continuously records the inside temperature. This data is collected at the end of the journey and checked to confirm that the travel conditions met our requirements and expectations.
Having arrived at one of the ports in China, our local team takes care of the product, so it again returns to our control. It is moved to bonded warehouses while it awaits CIQ clearance. These storage facilities are monitored for temperature and are kept as cool as possible.
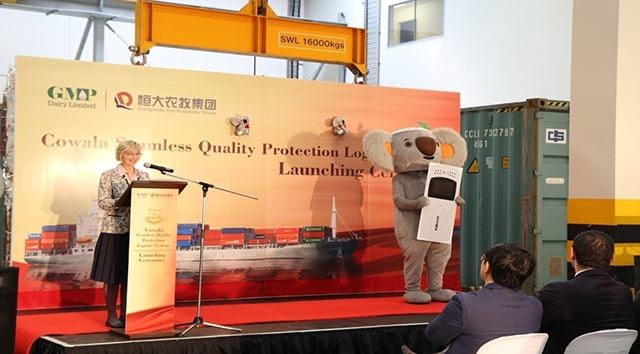
Evergrande GMP’s Seamless Quality Protection Logistic System
At time of manufacture, each and every can of Cowala product is batch coded with the usual information (Batch, Date of Manufacture, and Best Before) and in addition to this, each can receives its own unique 2D QR code – no two cans will ever have the same QR code. This is part of our patented “Black Box” system with which are able to link product information, raw material information, testing results, foreign matter detection images, and (in the unlikely event that we should we ever need it) recall information, to each individual can.
Anyone with the appropriate app on their smart phone can scan the QR code and will be directed to the website where are the relevant information is accessible.
The 2D code of each can is recorded as it passes along the production line and for the 6 cans in each shipper, there is a 2D code printed, denoting the 6 cans inside. At time of distribution, the code on the shipper can be scanned and the information is now available of which particular cans are being sent to which destination.
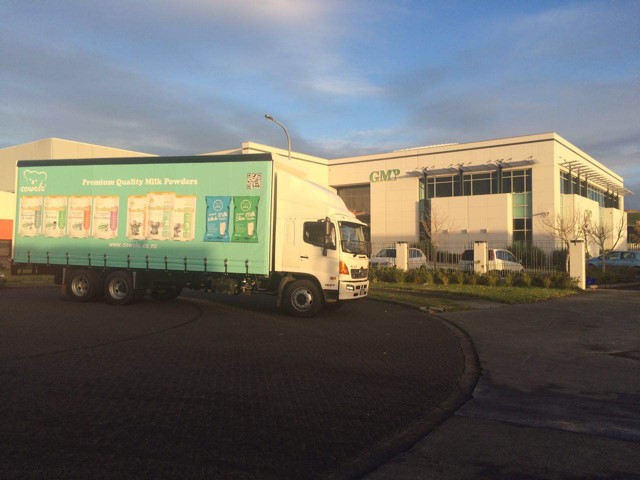